The spread of covid-19 outbreaks has led facilities in medical device manufacturing to rigorously anticipate, plan, and innovate. By Ali Burns, managing director of Siemens Healthineers Sudbury, UK manufacturing facility.
This is paid-for content from our commercial partners. Find out more
In its Sudbury facility, the work Siemens Healthineers does is intrinsically linked to the preservation of life; supply chains and distribution networks are constantly monitored and reinforced for the critical work the company undertakes.
Sponsored by
The facility manufactures blood gas benchtop products along with diabetes and urinalysis instruments. Even under normal circumstances, some of these are lifesaving machines, critical in hospitals and essential to patients’ survival. The covid-19 pandemic has made production of these instruments even more important.
With news of covid-19 spreading in other countries as early as January 2020, the site began preparations, increasing the raw material inventory to help protect production and maintain supply levels. This included several contingency planning meetings of the site leadership team, with a focus on keeping the Sudbury site running and ensuring that the business’s many customers could still obtain the consumables they needed. All manufacturers witness fluctuations in demand, and the need to anticipate, plan, and innovate is an established reality in medical device manufacturing.
The production challenge
As covid-19 outbreaks spread across the globe with increasing pace, the situation rapidly evolved from a distant threat into a global pandemic, bringing with it challenges on a scale the facility had never faced. With the acute effect of the virus on the respiratory system, the Ventilator Challenge UK Consortium was formed to scale up ventilator production in the UK.
Although the ventilator has received the most publicity in the covid-19 battle, the blood gas analyser has been equally important, the two instruments working together to read oxygen levels in patients’ blood at every stage of their journey through intensive care.
While the initial focus had been to protect existing production numbers, the facility was now faced with a very different challenge; it was being asked to build what would normally require a year in just two months.
In the space of a few weeks, the demand for blood gas products had doubled, trebled, and then almost quadrupled. To meet this demand, the facility increased production from 20 to 70 instruments per day. Demand for consumables skyrocketed as well, from nearly 20,000 to 32,000 units per month.
While the initial focus had been to protect existing production numbers, the facility was now being asked to build what would normally require a year in just two months.
The size of the task was monumental, with factory closures across the globe making sourcing parts even more challenging. The strategic procurement and materials teams worked tirelessly to source the parts needed, and there was also a real international effort from Siemens Healthineers to support the site.
Despite ongoing supply chain challenges, the facility successfully met these demands, more than trebling its output in a short time. Site leadership was proud to congratulate the entire team not only for meeting new production quotas, but also for keeping laboratories running with the consumables and systems they so desperately needed.
A united approach
It is said that crises can often bring out the best in people, and that has very much been the case in Sudbury. The facility could not have met the increased market demand and the pressures of redefining working processes overnight without the passion and sheer dedication of the workforce.
As a provider of critical healthcare products, the facility stayed open throughout the crisis, meaning that it put protective measures into place before the rest of the country. Staff rapidly adapted to a number of new procedures for their safety. This included a switch to shift work or working from home, more cleaners on site, limiting footfall in communal areas, a socially distanced minibus service, covid-19 training, and much more.
Staff united to achieve this, and employees did everything possible to support each other’s wellbeing, in recognition of the value of keeping morale high during these pressured times. The factory tannoys provided covid updates from leadership but were also handed over to staff to run quizzes and announce results from activities such as children’s colouring competitions.
Additionally, many staff were desperate to be part of the support effort, despite not being able to physically be on site due to shielding. Staff discovered and implemented new technology, such as HoloLens augmented reality, allowing new recruits to be trained remotely by experienced operators.
Celebrating the future
As a supplier of blood gas, urinalysis, and diabetes products, the Sudbury facility is well-acquainted with peaks and troughs in demand, but the pressures placed on it following the covid-19 pandemic have been truly extraordinary. Many positives have emerged from this crisis, but perhaps the most important is the way this shared experience has brought everyone in the facility closer than ever before.
Prior to the outbreak, the site celebrated its 80th anniversary. Since then, it has utilised new tools and reinvented processes, but looking forward to the next 80 years, it is the Sudbury staff that truly demonstrates the passion, resilience, and flexibility to tackle the challenges of the future.
For more information on point-of-care solutions from Siemens Healthineers, visit siemens-healthineers.com/en-uk/point-of-care-testing/critical-care-solutions.
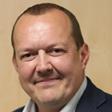